The circular economy of mineral wool
Our solution enables you to recycle 100% of the waste you generate producing mineral wool. The EcolBriq® technology enables us to make undersize bauxite particles and all production waste into briquettes.

EcolBriq®
Full value replacement of bauxite and basalt made from your waste and by-products
by EcolBriq®
waste
costs
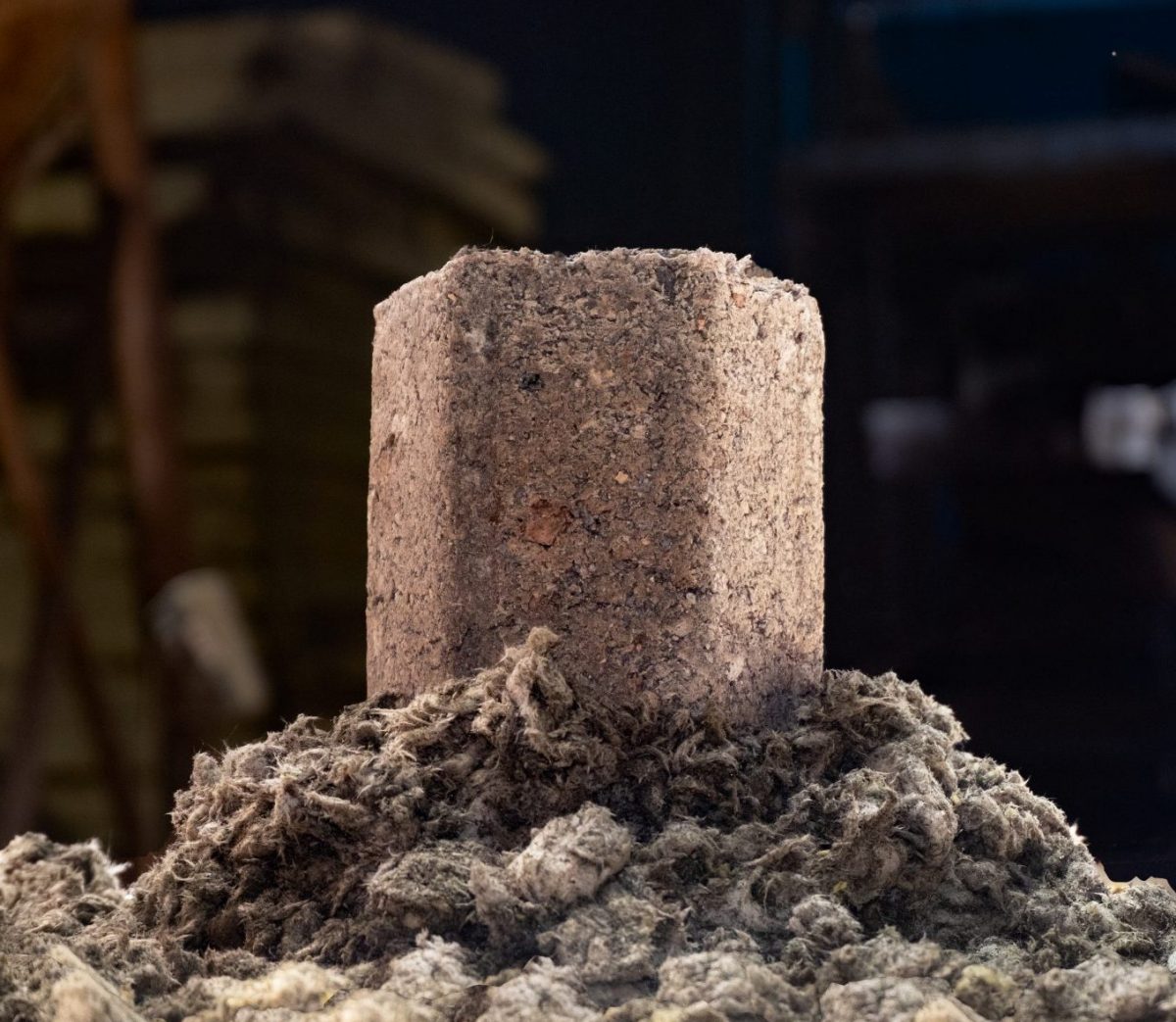
Profit from waste
We briquette the waste from your production processes to replace some of the feedstock in your furnace unit. EcolBriq® may include various types of mineral wool (including Grade II) as well as aggregates, blast furnace slag, bauxite, basalt, coke and other materials.
Benefits
- High-quality feedstock
- Reduced consumption of bauxite and other feedstock
- CO2 reduction
- Full recycling of production waste
- Dust reduction
Implementing zero waste operations
mineral wool, undersize bauxite and basalt particles
/year
not sent to landfill
per year prevented
since 2003